What is offline programming?
Offline Programming (OLP) or Offline Robot Programming (OLRP) software is a robot programming method that allows users to program their industrial manufacturing robot from a computer using software rather than using the robot controller. Using this method, manufacturers can keep their robot in production while programs are generated using computer software. This drastically reduces robot downtime, increases production efficiency, and saves on costs.
Manufacturing facilities around the globe are adopting automation to maximize their productivity and remain competitive. Manufacturing robots have many advantages such as high accuracy and consistent production which result in a much better ROI in comparison to completing processes manually. Robots do have a downside, however, when it comes to programming—most of the time, they must be offline to be updated or programmed, which means production delays and lost revenue.

How does offline programming work?
OLP software works with 3D CAD models to define tasks such as path planning, programming, and engineering.
The OLP environment utilizes a 3D CAD model of the robot work cell. All the programming is completed in the virtual space, which allows for troubleshooting and problem solving before the robot has been installed. Programs can be created, simulated, and edited in the OLP environment, ensuring that the robot will perform as required. Once the robot code is generated it's then uploaded to the robot.
Key advantages of offline programming vs teach pendant programming
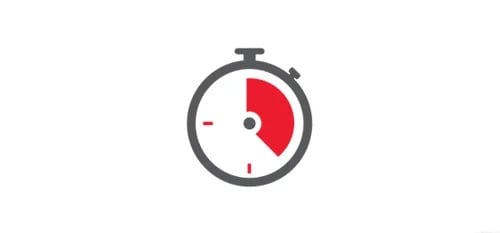
Quicker robot integration
Whether a new installation or a redeployment, time is always an essential factor. By creating, adjusting, and testing the programming in a virtual environment, when the robot is installed, it is ready to operate, saving days or weeks compared to a teach pendant.
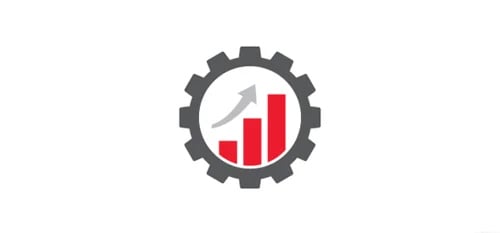
No downtime
With teach pendant programming, the robot must be in teach mode. OLP can upload the programming to a robot while it is operating, which means less manufacturing delays.
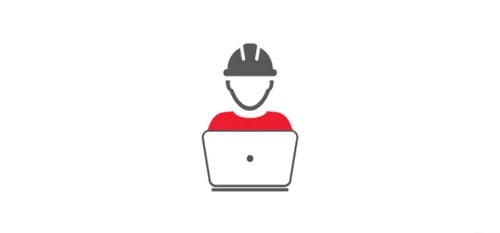
Safety
Whether faced with a safety concern due to robot configuration, or restricted access to the robot due to work from home protocols, OLP can be completed from a laptop in a safe location and uploaded to the robot without the need to access the teach pendant.

Quick changeovers
OLP can program a robot for part B, while it is completing the part A run. As soon as part A is complete, the part B programming can be uploaded and the task begun without turning off the robot. OLP allows for quicker cycle times, allowing for a higher mix of jobs with faster transitions.
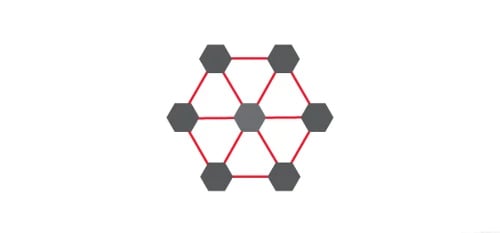
Universal application
Few manufacturing operations ascribe to brand loyalty, operating only one brand of robot. For most, the robot that accomplishes the task at the best price is the one that is installed, which leads to a variety of robots that need to be programmed. True OLP software should be “robot agnostic”, meaning it can generate code for a variety of robot brands.
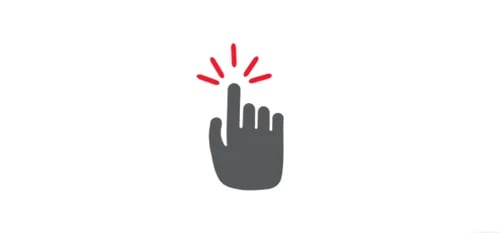
Ease of use
The right OLP requires process knowledge, however, it does not require advanced programming or robotics expertise. OLP is built around the user and is designed to be a clean and elegant user experience. In addition, the ability to interface with various brands of robots, your programmers do not need to learn proprietary OEM interfaces for each OEM robot brand.
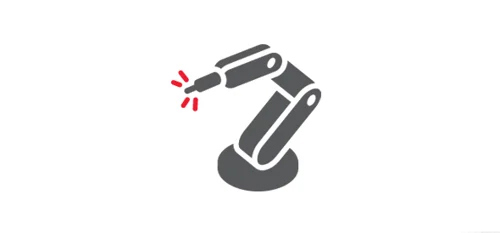
Test new configurations
Adding a robot into your manufacturing operation is a significant capital investment. OLP software should have an intuitive user interface that allows the user to design and test various configurations in 3D simulation before the robot is installed. Engineer, identify, and solve issues before the robot arrives.